1. What is DDP?
Diamond Dotted Insulation Paper (DDP) is a specialized insulation material made by coating electrical insulation paper with a diamond-patterned modified epoxy resin. At room temperature (below 30°C), it remains inert, dry, and non-sticky, making it ideal for transformers, motors, and other high-voltage electrical applications.
DDP is also known by various names, including Epoxy Adhesive Diamond Paper, Diamond Dotted Presspaper, Double-Sided Diamond Pattern Paper (DDPP), DPRCP, D.D.P, DPP, Diamond Dotted Insulating Paper, and Varnished Paper. It gets its name from the diamond-shaped resin pattern printed onto the insulation paper.
2. Key Features of DDP
(1) Diamond-Dotted Adhesive Design
The epoxy adhesive is applied in a diamond pattern on both sides of the paper, with each diamond measuring 9.5mm x 9.5mm and spaced 15.9mm apart. This design allows for proper oil penetration and gas release within insulation materials, effectively preventing corona discharge and partial discharge, ensuring the safety and reliability of the insulation structure.
(2) Superior Electrical Insulation & Mechanical Strength
When in use, the epoxy resin coating melts at a certain temperature during the coil drying process, creating adhesion. As the temperature increases, it cures, bonding adjacent layers into a solid unit. The adhesive strength of the epoxy resin is sufficient to prevent displacement of winding layers during short circuits, ensuring long-term mechanical and electrical performance.
(3) Excellent Heat & Moisture Resistance
Thanks to its high-quality base material, DDP maintains stable insulation performance even in high-temperature and high-humidity environments. This makes it ideal for electrical equipment operating in challenging conditions, such as humid environments.
(4) Easy Processing
DDP is highly flexible and can be easily cut, laminated, and bonded to meet various insulation needs. As a leading manufacturer of insulation materials, GBS offers tailored solutions based on your specific application requirements.
3. Applications of DDP
(1) Oil-Immersed Transformer Coil Insulation - Used for inter-turn insulation in power transformer coils and layer insulation in distribution transformers.
(2) Cable Shielding & High-Voltage Electrical Equipment - Serves as an anti-corona material for high-voltage motors and electrical components.
4. How is DDP Applied to Windings?
At high temperatures, the latent adhesive in DDP permanently bonds conductors into a solid unit. When heated to 90°C, the diamond-patterned resin melts, then solidifies in a single process. After 90 minutes at 90°C, the epoxy resin securely adheres to adjacent cables and insulation paper. The bonding strength reaches 70 psi (approximately 0.275 MPa, per U.S. standards) at 100°C.
Proper processing is critical when applying DDP. Improper adhesion or drying may cause insulation layers to detach from windings, leading to voltage breakdowns or partial discharges. Additionally, residual moisture in DDP can lead to water formation in oil-based materials, reducing transformer lifespan.
5. Factors Affecting DDP Pricing
(1) Raw Material Costs - The quality of the base paper and adhesive directly impacts the performance and price of DDP insulation paper.
(2) Manufacturing Process - The complexity and precision of production influence overall costs.
(3) Market Supply & Demand - Market fluctuations directly affect DDP pricing.
(4) Brand & Quality - Premium brands and high-quality products generally carry a higher market value.
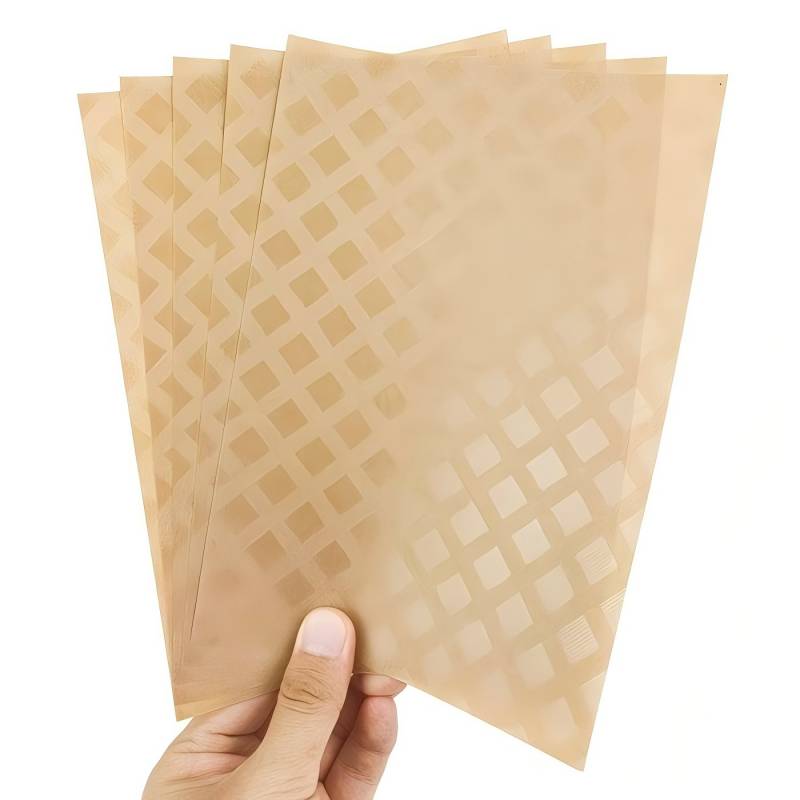
Post time: Apr-02-2025